Polo Automotivo Fiat, em Betim: fábrica de carros e centro de desenvolvimento em um só lugar
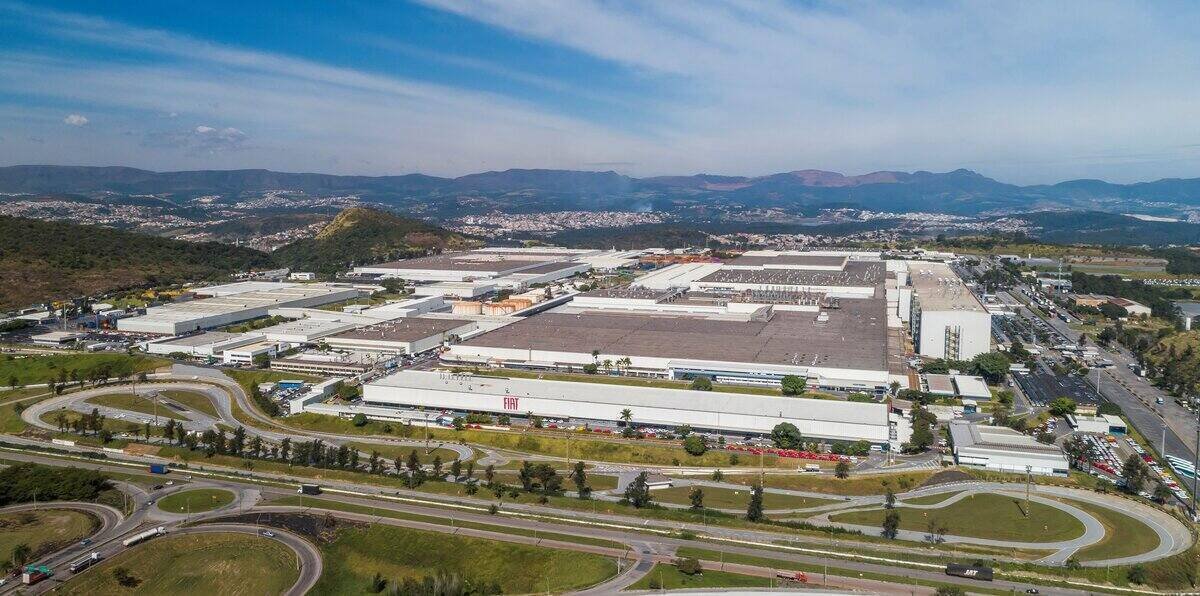
Sem tempo para ler? Que tal OUVIR esse texto? Clique no play!

O sucesso de uma montadora no Brasil, com produtos de vanguarda e de alta tecnologia, está diretamente relacionado a um parque industrial muito bem estruturado e que acompanha as mudanças dos novos tempos. Desde que inaugurou a fábrica de Betim (MG), em 1976, a Fiat sempre manteve suas instalações alinhadas à modernidade que o setor automotivo exige.
Ao longo de 45 anos, o Polo Automotivo Fiat foi ganhando melhorias, com investimentos volumosos e colocando em prática os conceitos da quarta revolução industrial, a chamada Indústria 4.0. Depois de receber R$ 7 bilhões para sua modernização, o complexo de 2,25 milhões de metros quadrados detém todas as tecnologias e recursos necessários não só para a produção de automóveis, mas também para o desenvolvimento de um novo veículo.
LEIA TAMBÉM:
> Como nasceu o pioneirismo mineiro da Fiat, que é a cara do Brasil
> Linha do Tempo: veja os principais marcos da história da Fiat no Brasil
Braço importantíssimo da gigante Stellantis, o polo de Betim chegou a produzir 3 mil veículos por dia em seu apogeu. Hoje, com capacidade para montar 800 mil unidades por ano, ele agrega processos inteligentes que garantem total qualidade tecnológica, capaz de fazer frente às fábricas mais avançadas do mundo.
Apesar das transformações em mais de quatro décadas, Betim segue olhando para o futuro. Todos os laboratórios, departamentos e linhas de montagem comprovam o caráter inovador do complexo. O laboratório Manufacturing 2020, por exemplo, é um setor destinado a experimentações, treinamentos e parcerias com as áreas de produção. “O pioneirismo está no centro da evolução da manufatura”, afirma Marcelo Lima, coordenador do Manufacturing 2020, que desenvolve dezenas de projetos simultaneamente. Os robôs são parte essencial da linha de produção de Betim
Um deles chama-se manufatura aditiva. Uma impressora 3D imprime desde engrenagens minúsculas a peças de 40 cm³, em 13 tipos de materiais plásticos. A máquina pode produzir 132 componentes e reduz em até 50% os custos das peças vindas de fornecedores.
Para a Fiat, investimentos periódicos significam um polo forte e produtivo, pronto para desenvolver toda sorte de projetos. Para se ter ideia, um aporte de R$ 500 milhões foi destinado para a linha de produção dos novos motores GSE Turbo de três e quatro cilindros, inaugurada neste ano por Carlos Tavares, CEO mundial da Stellantis.
MAIOR POLO DE MOTORES E TRANSMISSÕES DA AMÉRICA LATINA
A nova fábrica de motores eleva Betim como o maior polo de motores e transmissões da América Latina. De lá, podem sair 1,3 milhão de unidades por ano. A injeção de recursos aumenta a capacidade de exportação de Betim, que já tem compromisso formalizado de mandar, até o próximo ano, 400 mil motores principalmente para países europeus.
“A qualificação da mão-de-obra brasileira foi decisiva para trazer esse investimento para cá, pois outros países disputavam a fábrica de motores turbo”, afirma Antonio Filosa, presidente da Stellantis para a América do Sul.
O histórico também contribuiu para instalar a fábrica de motores em Betim. “O local tem forte cultura industrial de motores e transmissões e muita sinergia com as linhas de produção de outras famílias de propulsores”, explica Claudio Rocha, diretor de manufatura de powertrain América Latina. “A linha de produção já nasceu no contexto da Indústria 4.0, no qual predomina a conexão entre pessoas, máquinas, dados e inteligência artificial.” Esse cenário, aliás, inclui a aplicação de robôs colaborativos, sistemas avançados de controles do processo e incremento das tecnologias para reduzir o consumo de energia. A sala de realidade virtual ajudou a projetar até a linha de produção da nova fábrica de motores
Os recursos direcionados ao polo industrial de Betim vão muito além do desenvolvimento de novos motores. Em 2019, a Fiat investiu R$ 40 milhões, entre infraestrutura, equipamentos de última geração e treinamento, para inaugurar o Safety Center, moderno espaço dedicado à segurança veicular. Parte integrante do Centro de Pesquisa & Desenvolvimento Giovanni Agnelli, o Safety Center era a peça que faltava para a empresa ser capaz de projetar um veículo do início ao fim.
MAIS RAPIDEZ NO DESENVOLVIMENTO
Com 7.600 m², o Safety Center executa testes de impacto de até 4 toneladas a 100 km/h e simula uma série de situações, além de avaliar a estrutura do automóvel, a calibração dos airbags e os sistemas de retenção dos ocupantes.
“O Safety Center aumenta a agilidade no desenvolvimento dos automóveis, sem perder de vista os níveis de segurança exigidos internacionalmente”, revela Marcio Tonani, diretor dos Centros Técnicos de Engenharia para a América do Sul. Safety Center: testes de impacto de até 4 toneladas a 100 km/h
Antes do Safety Center Betim, todo veículo produzido na América Latina era enviado aos laboratórios da companhia na Europa ou nos Estados Unidos. “Agora, ganhamos autonomia e reduzimos o tempo na concepção de um automóvel”, acrescenta Tonini.
O centro está interligado à cadeia de desenvolvimento dos carros, desde a fase de conceito, passando pelas simulações virtuais, até chegar às provas físicas, homologação e início da produção. O uso da realidade virtual é um importante aliado, porque um modelo só é produzido depois de complexas análises em 3D, gerando economia e menos necessidade de ajustes.
Mas, antes de se submeterem aos testes de impacto, os carros dão seus primeiros sinais de vida no novo Design Center Latam, considerado o maior estúdio de design automotivo da América Latina. Com aproximadamente 150 profissionais responsáveis pela criação de projetos, o espaço exigiu investimentos de R$ 11,4 milhões. Design Center Latam é considerado o maior do tipo da América Latina
Em dois pavimentos que ocupam uma área de 2.700 metros quadrados, o Design Center herdou o know-how de 17 anos do Centro Estilo Fiat do Brasil. “Com uma equipe multidisciplinar de designers, engenheiros, sociólogos e psicólogos, o Design Center Latam faz intercâmbio com os polos de desenvolvimento da América do Norte, Europa e Ásia”, afirma Peter Fassbender, diretor do Design Center Latam.
Um dos diferenciais do local é o laboratório de User Experience (UX Lab), equipado com simuladores que testam soluções de interfaces e conectividade, além de percepções do design interno e externo dos veículos. “O UX Lab nos garante que o olhar de experiência do usuário esteja no processo de desenvolvimento e dentro de uma perspectiva de segurança”, explica Leandro Alvarenga, líder da área de UX.
Os simuladores reproduzem condições variadas de trânsito, como ultrapassagens, movimentação de pedestres, acelerações e freadas. O UX Lab não é a única joia da coroa do Design Center Latam. Há também a Sala Virtual com projetor laser de tecnologia avançada, que custou R$ 1 milhão. O equipamento projeta, em altíssima resolução, os veículos em tamanho real e os detalhes específicos de textura, o que proporciona análises mais próximas da realidade.
PLATAFORMA MLA ESTREIA NO PULSE
Anexo à Sala Virtual e ao UX Lab, o Showroom é o palco das apresentações de cada etapa dos projetos, até à aprovação final. A iluminação difusa valoriza a forma e as cores dos modelos.
Mas um dos mais recentes investimentos do polo de Betim foi a criação do Virtual Center Latam. A um preço de R$ 4 milhões, ele é considerado o mais completo do setor automotivo na América Latina. “Mais de 90% do desenvolvimento da nova Strada ocorreu na realidade virtual, com simulações de durabilidade, ruído, vibração, conforto térmico, aerodinâmica e segurança”, revela Filosa.
O Virtual Center Latam é dividido em três ambientes. A Sala de Realidade Virtual possui um software de última geração para criar modelos digitais imersivos, expostos em uma tela de 150 polegadas 3D. Na Sala Integrada, a realidade virtual é em 4D e as interações acontecem a partir de um cockpit adaptável, composto por chassi, bancos dianteiro e traseiro, painel, console e volante. Já a Oficina inicia a construção dos modelos físicos, onde os cálculos certificados nos dois estágios anteriores começam a ganhar vida.
O futuro de Betim também aponta para o que a empresa considera como uma nova plataforma, a do Progetto 363, o novo SUV Fiat Pulse, que na verdade é uma evolução da plataforma usada na família Argo. “A MLA (modular architecture) é a melhor resposta para os futuros carros, com novas unidades de potência, exigências de dirigibilidade, de conforto e de segurança”, avalia Marcio Tonani.
Ele conta que a MLA vai oferecer modularidade capaz de suportar não só os desafios que os veículos terão daqui para frente, como também assegurar a competitividade técnica dos modelos produzidos no polo automotivo de Betim.
SEM INTERFERÊNCIAS ELETROMAGNÉTICAS
Não adianta um carro de alto nível ser alvo fácil de interferências eletromagnéticas. Para evitar isso, a área de Engenharia de Eletro-Eletrônica de Betim trabalha com oito laboratórios equipados com tecnologia de ponta para realizar testes que promovam a melhor experiência ao usuário.
Os laboratórios avaliam a compatibilidade eletromagnética em uma sala projetada e com câmara semianecoica blindada, que mede frequências contínuas de 0 GHz até 10 GHz, a fim de conter ondas eletromagnéticas e suas possíveis interferências. As paredes são isoladas com espuma composta de carbono e tinta especial, garantindo ao ambiente a maior pureza possível. Ao blindar sinais, como de GPS e celulares, os testes transmitem informações precisas sobre o funcionamento das centrais multimídias. Laboratório analisa interferência eletromagnética nos componentes dos veículos
Existem dois tipos de interferências eletromagnéticas que precisam ser testadas: as conduzidas, que passam nos cabos elétricos dentro do carro e que podem causar danos elétricos, e as irradiadas, provocadas por ondas eletromagnéticas que geram interferências e danos elétricos. O objetivo das análises é fazer todas as medições e se certificar que os componentes do veículo não vão sofrer e causar interferências.
Ao adotar práticas tão modernas da Indústria 4.0, Betim levou o conceito de avanço tecnológico até para o trabalho cotidiano dos funcionários. Ela foi pioneira no uso do exoesqueleto, incorporado ao processo produtivo. Essa espécie de esqueleto-robô, leve e de fácil adaptação, sustenta o peso do operador de manufatura para reduzir seu esforço muscular e melhorar sua condição ergonômica. Funcionário veste o exoesqueleto, que ajuda a aliviar o peso suportado pela musculatura
Em situação em que o trabalhador precisa flexionar as pernas, por exemplo, o peso do tronco é absorvido pelo exoesqueleto. A vestimenta biomecânica parece um colete e carrega o peso do usuário, que chega ao final da jornada de trabalho mais descansado, já que há uma redução das cargas suportadas pela musculatura do funcionário.
A preocupação com a saúde ocupacional também é medida em avaliações dos funcionários por meio de uma câmera termográfica. Os tecidos inflamados acusam temperatura mais alta e a termografia dá o sinal de alerta, permitindo uma intervenção médica preventiva. A tecnologia consegue analisar vasos sanguíneos, tendões, músculos e inervação, que são estruturas envolvidas na biomecânica das atividades.
LEIA TAMBÉM:
> Como nasceu o pioneirismo mineiro da Fiat, que é a cara do Brasil
> Linha do Tempo: veja os principais marcos da história da Fiat no Brasil