Método, que usa ferramental maior, pode reduzir pela metade custo de produção de um carro elétrico
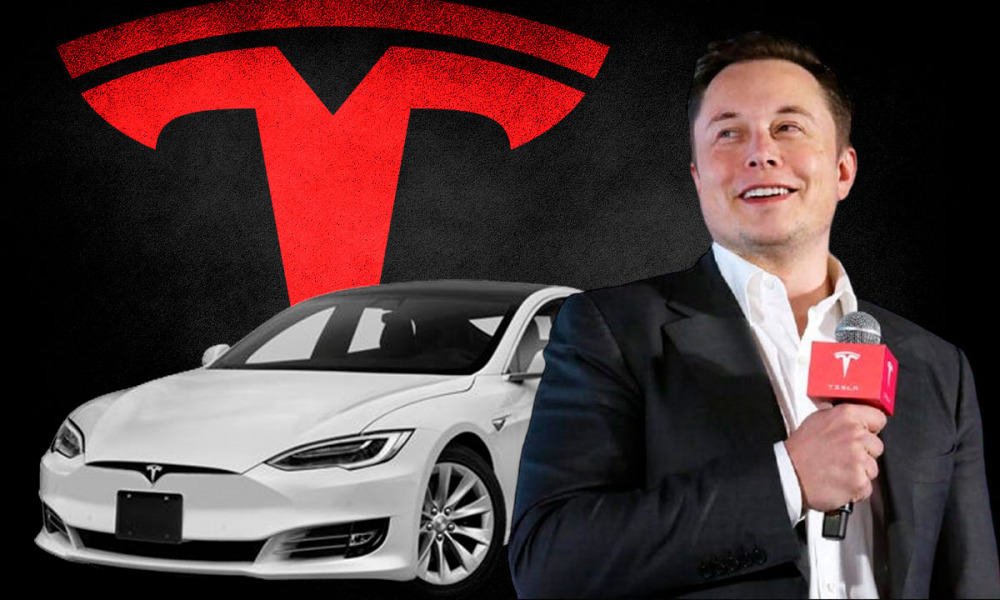
A Tesla desenvolve um novo sistema de produção que pode reduzir pela metade os custos com a fabricação de seus carros elétricos.
Uma nova tecnologia permitirá à montadora fundir quase toda a complexa parte inferior da carroceria de um veículo elétrico em uma única peça. No carro convencional são cerca de 400 peças nesta área da carroceria.
O Lego da Tesla?
O know-how é fundamental para a estratégia de fabricação “unboxed” da Tesla, revelada pelo CEO Musk em março, um eixo de seu plano de produzir dezenas de milhões de veículos elétricos mais baratos na próxima década e ainda obter lucro.
– Faça a sua inscrição no #ABX23 – Automotive Business Experience
Embora a Tesla tenha dito que seu modelo envolve a produção de grandes subconjuntos de um carro ao mesmo tempo e depois juntá-los, o tamanho e a composição dos blocos modulares ainda são objeto de especulação.
Terry Woychowski, presidente da empresa de engenharia norte-americana Caresoft Global, afirma que se a Tesla conseguisse fundir a maior parte da parte inferior de um EV, isso mudaria a forma como os carros são projetados e fabricados.
VEJA MAIS:– Tesla quer montar 500 mil elétricos por ano na Índia– Tesla no centro de várias investigações nos EUA
“Tem uma enorme implicação para a indústria, mas é uma tarefa muito desafiadora”, disse Woychowski, que trabalhou para a montadora norte-americana GM por mais de três décadas. “Fundições são muito difíceis de fazer, especialmente as maiores e mais complicadas.”
Duas das fontes ouvidas pelo Automotive News disseram que as novas técnicas de design e fabricação da Tesla significam que a empresa poderiá desenvolver um carro do zero de 18 a 24 meses. A maioria dos rivais atualmente leva de três a quatro anos.
Uma única estrutura grande – combinando as seções dianteira e traseira com a parte inferior da carroceria central, onde a bateria está alojada – poderia ser usada no veículo compacto que a Tesla pretende lançar por um preço de US$ 25 mil até meados da década.
Esperava-se que a Tesla tomasse uma decisão sobre fundir a plataforma inteira já em setembro de 2023, disseram três das fontes. Mesmo assim, o produto final poderá mudar durante o processo de validação do projeto.
Nem Tesla e nem Elon Musk, CEO da companhia, se manifestaram sobre a reportagem.
Criar moldes grandes traz inúmeros risco ao projeto
A inovação da Tesla se concentra na forma como os moldes gigantes para uma peça são projetados e testados para produção em massa. E como as peças fundidas podem incorporar chassis auxiliares ocos com nervuras internas para reduzir o peso e aumentar a resistência a colisões.
Em ambos os casos, as inovações, desenvolvidas por especialistas em design e fundição na Grã-Bretanha, Alemanha, Japão e EUA, envolvem impressão 3D e areia industrial.
Até agora, as montadoras têm evitado fundir estruturas cada vez maiores por causa do “dilema do gigacast”: criar moldes para fazer peças de 1,5 m² ou mais aumenta a eficiência, mas tem alto custo e traz inúmeros riscos.
Custo menor nos ajustes do ferramental
Depois de pronto o ferramental, os ajustes de usinagem durante o processo de projeto requerem investimentos de US$ 100 mil, por tentativa. E refazer o molde por completo pode custar US$ 1,5 milhão, de acordo com um especialista em fundição.
Outra fonte disse que todo o processo de design de um grande molde de metal normalmente custa cerca de US$ 4 milhões.
Isso foi considerado proibitivo pelas montadoras – especialmente porque um projeto pode precisar de meia dúzia de ajustes ou mais para alcançar uma matriz perfeita do ponto de vista de ruído e vibração, ajuste e acabamento, ergonomia e resistência a colisões.
Mas a visão de Musk desde o início era encontrar uma maneira de moldar a parte inferior da carroceria inteira, apesar dos riscos.
Tesla usa impressão 3D e areia para molde
Para superar os obstáculos, a Tesla recorreu a empresas que fabricam moldes de teste a partir de areia industrial com impressoras 3D.
De acordo com uma fonte, o custo do processo de validação do projeto com fundição em areia, mesmo com múltiplas versões, é mínimo – apenas 3% de fazer o mesmo com um protótipo de metal.
Isso significa que a Tesla pode ajustar protótipos quantas vezes forem necessárias, reimprimindo um novo em questão de horas.
O ciclo de validação do projeto usando fundição em areia leva apenas de dois a três meses, em comparação com algo entre seis meses a um ano para protótipos de moldes de metal.